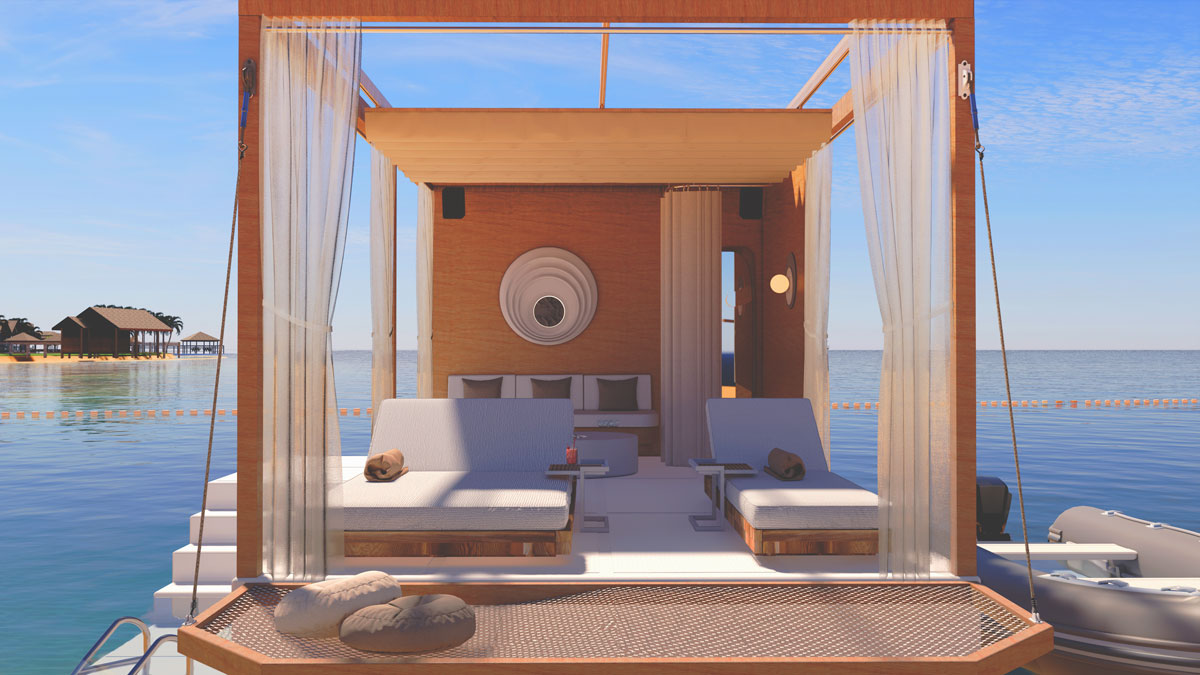
Beach holidays are no longer limited to the traditional trio of sea, sand, and sun. Today’s travelers crave unique experiences that blend relaxation with innovation. Enter the Floating Lounge, an innovative addition to waterfront properties [...]
Floating docks are designed and produced with special materials according to conditions and needs. Because they float, they can rise and fall with the water level above the body of water. This feature makes them different from fixed docks.
Floating docks can be manufactured from various different structural materials, and are mainly used as a passage between land and water.
In general, there are five types of floating docks (dock options):
• Concrete Pontoons
• Aluminum Pontoons
• Steel Framed Docks
• Rotational HDPE Plastic Docks
• Polyethylene Pontoons
Consider the location of the project when choosing a floating pontoon. This will help determine the wind and wave loads in that area. Then the suitable pontoon which will best accommodate these loads is selected. Once the type is selected, it will then be manufactured as per the client/project’s requirements and needs.
The use and purpose of each of the above-mentioned models does vary. In this article, we will talk about the features of pontoon models that are generally used in the market.
Manufacturers use a water-resistant, T6 marine Aluminum to create aluminum frame docks. The structure is usually fitted with wooden or composite decking. Floats used are made of high-density polyethylene or fiber-concrete-covered EPS.
The pontoon's design is unique in that it has channels that allow for cleats and fenders to be securely attached, while also allowing for easy modification of the equipment on board. Floating aluminum pontoons are light, mobile, and can be shipped worldwide either by container or by land.
Floating aluminum docks are suitable for fresh or salt water. They are generally used in shallow waters (calm waters) within the port as the wave strength is not high in the closed water area. They are mainly used as piers for marina and boat mooring, and floating walkways.
The Aluminum pontoon is the most expensive among the pontoon types, and that is due to aluminum chassis raw materials requiring decking and craftsmanship which increases the cost. Polyethylene floter is a common choice. To protect buoyancy in case of cracks, these blocks must be filled with EPS Styrofoam. This model has a commercial life of up to 20-25 years.
Carrying Capacity: Medium 3 Points
Aesthetics: High Standard 5 Points
Practicality: Functional to use 4 Points
Commercial Life: 20 – 25 years commercial life 3 points
Cost: High 2 Points
Wave Resistance: Low 2 Points
Concrete pontoons are the best solution for high amplitude purposes. The concrete bulk system is fitted around a high-density EPS core.
This forms an economical and durable block in one piece. All of the iron reinforcement parts used for this single-piece pontoon block are hot-dip galvanized. Sulfate resistant CEM3 class concrete is the preferred type used in the manufacturing process. Using these raw materials enables the concrete and steel parts to become resistant to corrosion.
Floating concrete pontoons have the highest load capacity, wave resistance, and commercial life of all pontoon models. They can be used in many different areas, such as marinas, floating platforms, and floating house/restaurant/office foundations. They are also suitable for military and floating docks.
Carrying Capacity: High 5 Points
Aesthetics: Standard 4 Points
Practicality: Functional to use 4 Points
Commercial Life: 40-50 years 5 points
Cost: Reasonable 4 Points
Wave Resistance: High 5 Points
This type of dock (pontoon) is made by heating the plastic raw material to liquid which moves then into a mold on multi-axis rotation. These products are generally interconnected and are 3mm to 8mm thick. Plastic docks are mainly used as a surface platforms on the water for areas that are periodically and temporary used for swimming purposes.
Plastic pontoons are preferred for easy installation and low cost. However, the commercial life is quite short. The plastic heats up and cools down under the sun. This causes it to lose its flexible properties.
Capillary cracks then start to form. The water starts to seep into the pontoon modules. That could cause the pontoon to either sink or lose its carrying capacity with the force of the other blocks completely.
Carrying Capacity: Low 2 Points
Aesthetics: Low 2 Points
Usability: functional 3 Points
Commercial Life: 2-3 years 2 points
Cost: Low 5 Points
Wave Resistance: Good 4 Points
Although similar to the floating aluminum pontoons, they are manufactured using structural steel. All steel parts are coated with hot-dip galvanized to protect against corrosion. This type of pontoons are usually used as a better alternative to plastic while maintaining similar costs.
The steel frame carcass is highly resistant to flexing, and fiber concrete floats are used underneath it. Natural wood or WPC composite coatings are preferred decking on the steel frame. This pontoon model is suitable for circular and asymmetrical architectural needs, as the steel frame can be curved into different shapes.
Floating steel docks are generally used for touristic swimming facilities, boat berthing, floating platform, finger pontoon, sunbathing island, etc…
They are very comfortable in point loads as the carrying capacity of the pontoon blocks are connected to each other. Steel pontoons work rigidly as a single piece. Steel dock have a commercial life span of 10 to 15 years, but could be slightly higher in freshwater basin.
Carrying Capacity: Medium 3 Points
Aesthetics: Medium 3 Points
Usefulness: Functional 4 Points
Commercial Life: 10-15 years 3 points
Cost: Low 5 Points
Wave Resistance: Medium 3 Points