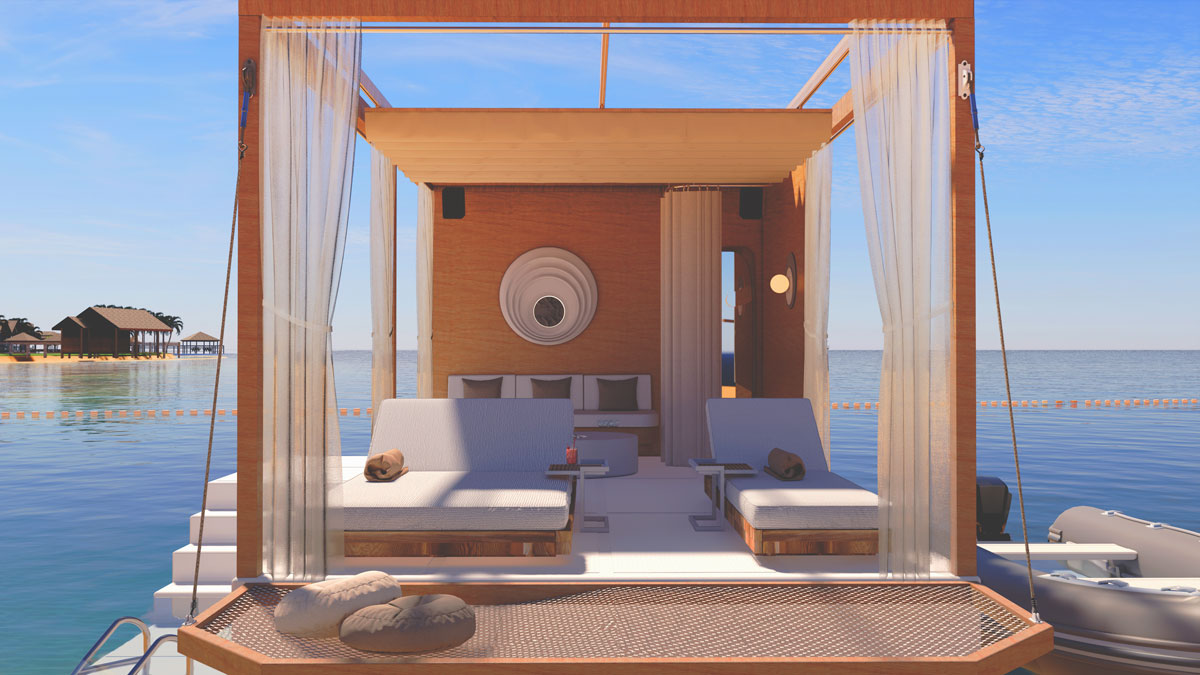
Beach holidays are no longer limited to the traditional trio of sea, sand, and sun. Today’s travelers crave unique experiences that blend relaxation with innovation. Enter the Floating Lounge, an innovative addition to waterfront properties [...]
Floating breakwater and wave attenuator systems are used to protect marina and harbor structures from wave and external influences. Wave damping characteristics of floating breakwaters vary according to the wave period and wave height. They have 90 to 100% wave retention in short and medium period wave formations. They also show damping of up to 80% in long period waves occurring in high seas.
There are 2 types of breakwaters that are accepted and used frequently in the world. These breakwaters can be defined as T type and U type.
T-Type breakwaters are especially used in watersheds with short periods and wave heights of up to 110 cm. The T-type breakwaters are able to damp the resulting waves by 90%. Width and depth of the structure to be used are determined according to the wave and wind analysis.
U-type breakwaters are used to a greater extent in construction and are preferred. Floating breakwater models are manufactured in widths from 3 to 10 meters, and underwater depths from 1.5 to 3 meters. The U-type floating breakwater disrupts the mechanical structure of the incoming wave and absorbs its reflection to create a safe area within the harbor. Additional skirt curtains protruding from under the floating platform create a force contrary to the wave’s mechanics and prevent the passage of the wave. This type of breakwaters are used in short, medium and long period waves.
Floating breakwaters are ecological structures. The materials used are recyclable and do not release any harmful gas or create corrosion waste. When compared to fill-type or piled systems, these types of breakwaters do not harm the surrounding natural life, the micro-flora in the area, and the natural discharge directions. They do not pose any danger of environmental pollution during the construction and installation.
Floating breakwaters are also more beneficial in terms of financial efficiency than the conventional methods. Since the costs are much lower than those of the other methods, the return on the investments can be made in a much shorter time. Compared to conventional fill-type breakwaters, they takes up less space, are lower in cost, and can be used as a floating piers or docks without the need for additional berth fillings.
Floating breakwaters are mainly used to protect marina areas. Boats moored to the piers in the marina can be anchored comfortably. Floating breakwaters also significantly increase the capacity of marinas since they can be used as additional berthing places.
Such breakwaters are also a main part of port structures. They can be used in many areas such as fishing shelters, mine loading facilities, passenger ports, fish farms, water sports facilities and coastal erosion prevention.
Floating breakwater design is generated according to the various technical data. The most efficient breakwater model is designed taking into consideration technical data such as the underwater map of the place where the breakwater will be built, the basin distances that will produce wave formations, the maximum wave height and length, the wind and the binding loads.
Floating wave damping systems are basically fixed to each other by connection cables and shock-absorbing rubber pads. Materials used in the production are selected on the basis of 50 years of design and strength criteria.
Marine type sulphate-resistant concrete is manufactured in conformity with high pressure resistance. Hot-dip galvanized Steel reinforcement used in concrete are corrosion resistant and contribute to the longevity of the structure. EPS (expanded polystyrene) core used in floating breakwaters has high density and water absorption of up to 3%. Such breakwater structures can maintain a commercial life of up to 50 years.
The mooring system (anchoring) of floating wave prevention systems to the sea bed is a crucial issue that requires sound calculations, professionalism and experience. In general, the heavy chain is connected to the concrete anchors placed on the seabed. It is fixed to its position on water by cross and vertical connections.